北排研发中心王佳伟主任:打造梦想中的智慧污水处理厂(图)
此主题相关图片如下:
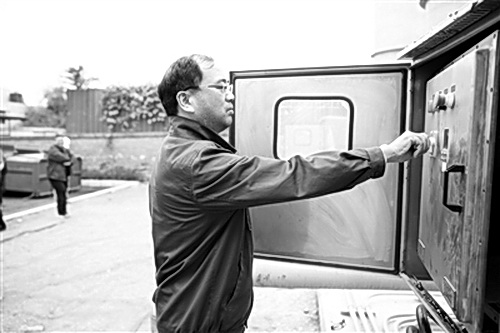
图为:北京排水集团科技研发中心主任王佳伟在做沼气尾气燃烧器点火实验。
(水业中国网上海工作站4月30日讯)如果可以通过技术,可以让机器设备自己适应污水变化,在污水处理过程中对各项参数进行智能估计,那么污水处理也就实现了智能化,进而打造智慧的污水处理厂。这是北京排水集团科技研发中心主任王佳伟的理想。在过去的十几年,他和同事利用所学,使污水处理厂利用先进的方法,初步实现了自动化控制,形成了智慧水厂的雏形。
摸索:自主研发沼气脱硫装置
2003年,王佳伟来到北京排水集团。他觉得自己很幸运,可以从事所学专业,并且进入了全国最早成立企业研发中心的北京排水集团。当时,北京排水集团刚刚立项新的科研项目:沼气脱硫。因为是第一家大规模使用厌氧消化的排水企业,新技术应用过程中,伴随着新的问题出现,需要一一破解。
“厌氧消化在当时是非常先进的技术,但是这个处理方法,在处理污水的过程中,会产生有毒有害气体,所以研究沼气脱硫专门成立了课题。”王佳伟说。
王佳伟清楚地记得,那是7月15日,刚刚离开校园来到企业,排水集团给出的时间是4个月,11月15日前必须实验成功,否则就要从其他行业引进技术。正值酷暑,白天,全副武装的王佳伟跟同事们一起在现场做实验,一次、两次、三次,一百次、二百次、三百次……到了晚上,进入实验室检测分析数据。到了10月,天气渐渐凉爽下来,实验终于有了些眉目。
“那年的雪下得特别早,11月初就下了第一场雪。”王佳伟说。当时,实验装置被雪盖住,大家一起扫雪,在寒冷的北风中做实验。到了11月10日,实验终于取得了稳定的效果,北京排水集团建成了自主研发的第一个沼气脱硫装置。
“排水这个行业不同于其他行业,其他行业自动化程度比较高,但污水本身具有腐蚀性,所以一些设备设施不太容易实现自动化,刚到排水集团的时候,绝大多数操作还需要人工完成。”王佳伟说。
如果从其他行业引进,每年脱硫的总成本大约在1000万元左右,而这套自主研发的设备,每年的总成本仅400万左右,这为排水集团每年节省成本500多万元。这开启了王佳伟污水资源化利用和节能降耗的研发、转化和产业化工作。
事实上,王佳伟一直在刻苦钻研,工匠创新。作为一名科研人员,他不断丰富专业知识,开展科学研究和创新工作,并树立了终生学习的学习理念,扎根基层。作为技术骨干,他先后承担了国家863计划、国家科技支撑计划、国家水专项、北京市科技计划等近十项省部级课题的研究工作,以解决国内污水处理厂处理设施能耗高、达标不稳定一系列问题。
研发:脱氮除磷节能控制系统
2005年,王佳伟开始研究脱氮除磷节能控制系统。这是一项基于国家布局,集团讨论的污水处理技术。这项现在看来非常容易的技术,在当时大家都不是很了解,怎么做心里没有底。污水处理是排水集团的主营业务,怎样升级提高水质、合理控制成本,正是脱氮除磷节能控制系统需要解决的问题。
处理设施能耗高、达标不稳定是国内污水处理厂一直存在的问题。王佳伟意识到要解决上述问题,必须实现污水处理的动态控制。但是由于污水行业污染物成分复杂、对在线仪表的腐蚀损害严重、水质水量变化大等特点,现有的自控技术难以成功应用于污水厂的生产实际。
王佳伟带领团队从零做起。他学习了自动控制原理、数学建模和互联网知识,并结合自己已有的污水处理专业知识,制造了全国最大的试验装置。刻苦钻研、努力实践、不断创新,往往在单位一干就是一天,试验数据一天就有几十个。
微生物和人一样,需要精细照顾,团队时时刻刻关注参数,白天黑夜盯着看。两三个人的团队轮流关注,每人盯十几个小时,取样、分析,干到凌晨几点都是很正常的事,没有周末的概念。就这样盯了一年半,每天取三四十个样,每个样分析三四种数据,数据量巨大。
而这只是第一步。如何将研究成果应用到厂里去,怎样与现有工艺结合?他主动到生产一线了解情况,跟工人和管理层打成一片,将控制系统的设计生产跟经验制度结合起来。2010年,他来到高碑店污水处理厂,带着任务,继续改造。
“跟工人们学到不少东西,工人更关注实际操作方便、指令准确这些非常具体的东西。”王佳伟说。
在这样的环境中,王佳伟的研究思路不断的成熟,最终开发了基于脱氮除磷原理的前馈模型和反馈调节相结合的优化控制技术,并结合互联网,实现了工业化和信息化在污水行业的融合,形成了具有污水行业特色的污水处理厂动态调度控制系统,这是国内首次实现水厂从单一污染物减排到多元综合利用的转变。
“排水行业,污水在任何时刻、任何地方、任何单位都收集回水厂处理,但出水标准是统一、一定、稳定的达标,这就对自动化控制要求非常高。污水脏臭腐蚀仪器仪表,造成数据可能不够稳定,以至智能化水平处理一直处于初级阶段,更多的需要人工干预。这是我们需要解决的问题。”王佳伟说。
以前除磷加药,需要工人去现场调,现在在机械上实现,加多少药可实现自动调整。工人们反映,有了这套系统,终于可以踏踏实实的工作了。人工干预减少,自动化程度提高。
这套系统以“精准配水、精准曝气、碳源优化、精准泥龄控制、厌/缺/好氧体积比控制”为核心技术,具有高效脱氮除磷、显著降低电耗、大大提高工艺的灵活性及稳定性等特点,形成了集技术方案与产品装备化为一体的相关技术。在技术开发过程中,培养和锻炼了紧缺的工艺和自控技术团队。上述成果获得了3项省部级奖,并获得了《第一批中关村国家自主创新示范区新技术新产品(服务)证书》、入选北京市发改委等七个委办局联合发布的《北京市节能低碳技术和产品推荐目录》,并已在北京高碑店污水厂、清河污水厂、小红门污水厂和全国部分污水厂推广应用,出水氮磷达标率提高20%以上,吨水电耗节约达到10%以上,每年产生经济效益1000万元以上,并取得了良好的社会效益。
梦想:污水资源化系统马车换汽车
北京排水集团科技研发中每年申请专利30项左右,全部具有知识产权保护,其中王佳伟负责的有五六个项目,20几名硕、博学历科研人员。如果说过往的科研成果使排水行业由人工转向了自动化的飞跃,那么现在的王佳伟,正在科研的道路上飞奔,他希望污水资源化利用可以由“马车”转变为“汽车”。而这,正是身为一名科研工作者的梦想。
新型污水资源化利用系统是王佳伟目前正在研究的技术。
“我们现在的污水处理技术,仍然是以微生物处理为主。污水中有上万种微生物,我们以前以及当下的技术,就好比用马车在拉车,而现在,我们想能不能用汽车,加快污水处理的速度和水平。”王佳伟说,“正渗透,是指通过某种设备和技术,直接把污水过滤,只需要几分钟,就可以把污水过滤干净。”
作为一名科研人员,王佳伟功底深厚,但他有自己的“永不满足”。坚持“创新”,是他对自己的要求,“创新”精神也浸润着他一路走来的轨迹。随着北京市污水资源化工作的深入开展,以活性污泥法为核心的现有深度处理技术普遍存在工艺操作控制不精确、占地大、流程长、能耗高等问题。王佳伟积极寻找解决上述问题的方案,确认国际上正处于研究前沿的正渗透膜分离技术对于污水中的污染物可进行直接分离,既易于精确控制,同时显著减少占地、并可完全开发污水中潜在的能源,实现高效节能的污水深度处理。因此,他将这一方向作为主攻方向,经过学习准备,2014年争取到了去哈佛大学等国际一流研究机构学习交流的机会,跟踪学习该项国际前沿技术并赴哈佛大学研修一年。
在国外,他抓紧每一刻时间,早上六七点就到实验室,晚上十点回到宿舍,无团队支撑,从装置搭建到数据分析全部自己动手。访学期间设计构建了以正渗透技术为核心的新型污水资源化利用系统一套,开展正渗透污水深度处理的试验研究,确定了正渗透技术的工艺操作参数、膜污染控制方法和系统处理效果。
由于这项技术在国外也是刚起步,王佳伟及时加入,使国内同步开展了研究:“目前我们仅仅是掌握了工艺参数,距离应用还需要做很多工作。技术一旦突破意义非常重大,好比一辆崭新的汽车。”
每天7点多到单位开始一天的工作,晚上七八点钟离开,即使回家也在琢磨科研难题,半夜醒来想起什么,赶紧起来记下。这是王佳伟的日常。“还是想要把水厂做得更智慧一些,能源化资源化一些,比如把污泥更多的产生沼气用于发电,处理过的有成分标准的污泥回到生态环境中进行土地修复,用于沙荒地改良,园林绿化。”作为一名青年科研工作者,王佳伟说,“不去干,问题永远在面前,每一个问题,都是我们努力的方向。”
(来源:新华网,作者:记者边磊摄影,上海供排水项目网戴晓红编辑,2019年4月30日)
「该帖子被 戴晓红 在 2019/4/30 20:53:13 编辑过」